Resources
What can we help you find?
News
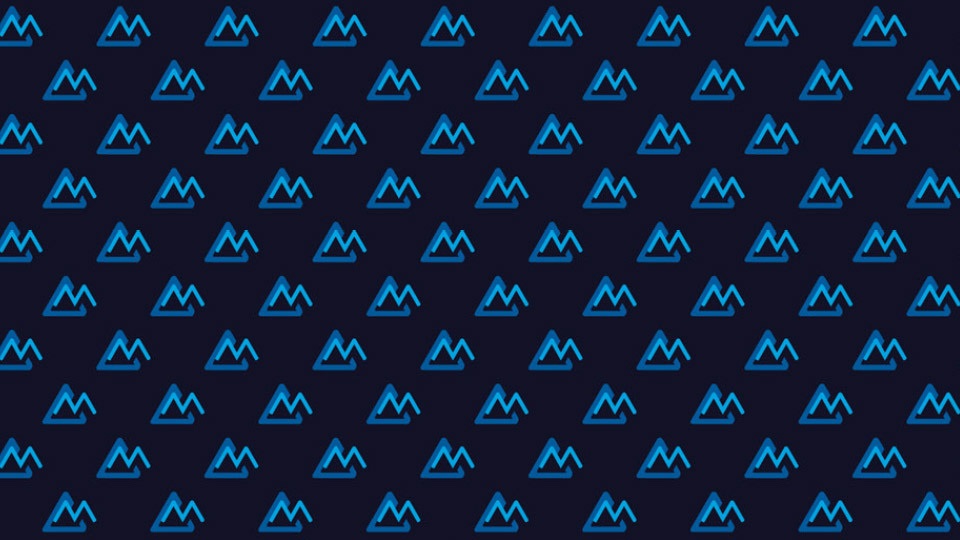
Net Zero: Clever OWL preys on recyclable net and tag coding packaging trends
Nov 07, 2022
Clearmark has mastered the challenge of efficiently over-printing watchstrap label bands on the uneven surface areas use...
Read full article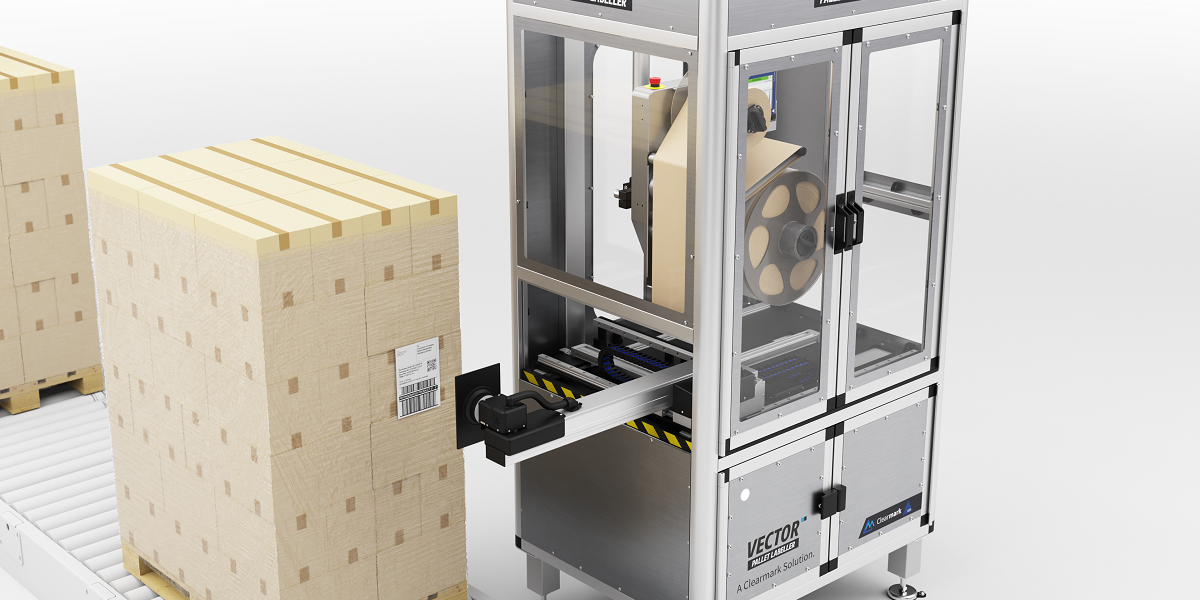
ICE Vector establishes Clearmark's foray into pallet labelling
Sep 21, 2022
The ICE Vector brings to the marketplace a new high performance, low maintenance tertiary option that is exceptionally e...
Read full article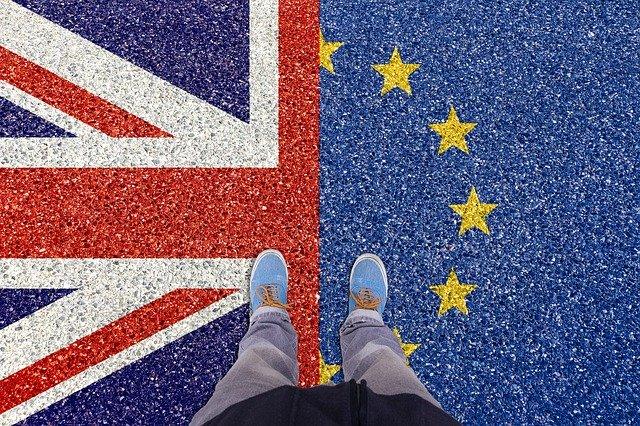
Brexit labelling changes for British produced foods sold into the EU
Jan 20, 2021
From January 1st 2021 there are significant legal changes to food labelling requirements for British goods exported to E...
Read full articleHow has the coronavirus pandemic impacted food manufacturing and consumption in the UK?
Dec 10, 2020
Looking at the impact coronavirus has had on Britain’s social norms, purchasing habits, food consumption, and the associ...
Read full article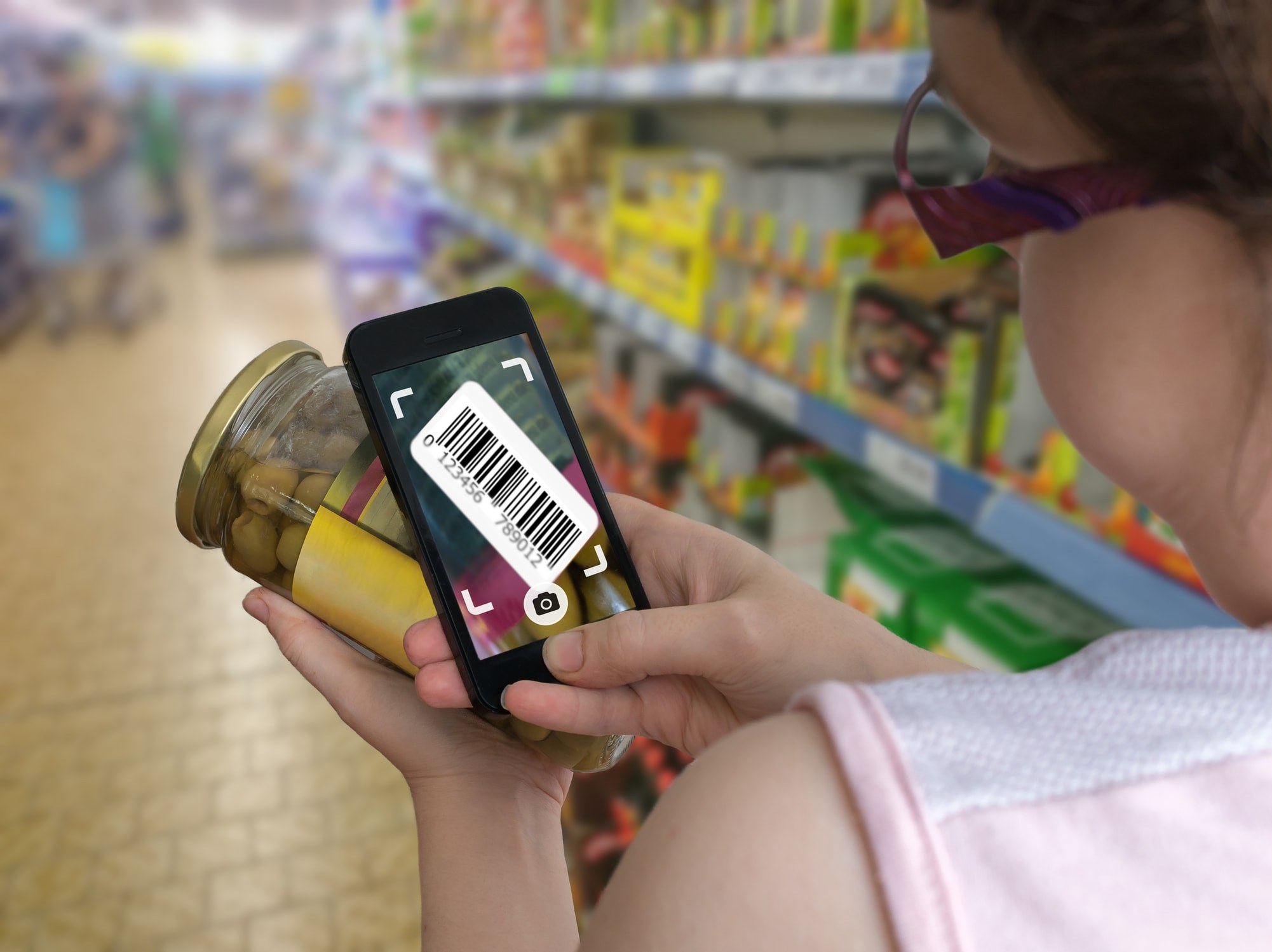
Smart Labels in the Food Industry: Applications and Benefits
Jun 27, 2020
‘Smart labels’ are the latest innovation within packaging that can be utilised by food manufacturers to improve traceabi...
Read full articleVideos
Guides
Success Stories
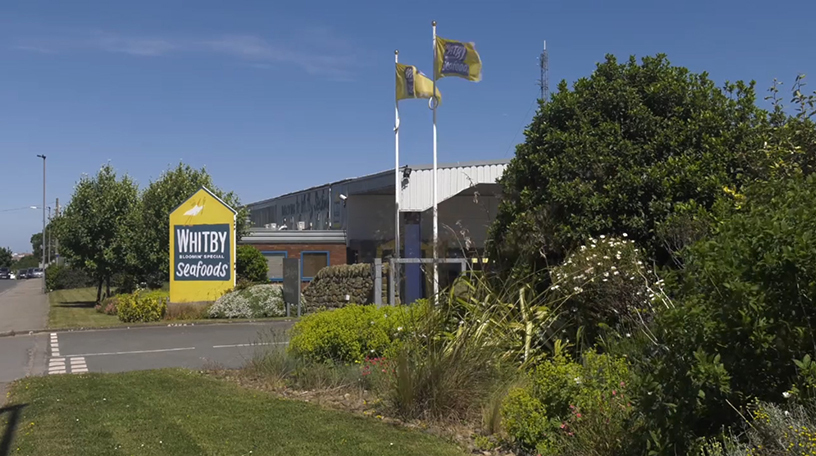
Clearmark’s accurate and flexible coding solution proves the perfect catch for Whitby Seafoods
With Whitby’s legacy equipment struggling with reliability and throughput, Clearmark identified that its ICE Thermal Tra...
Read Success Story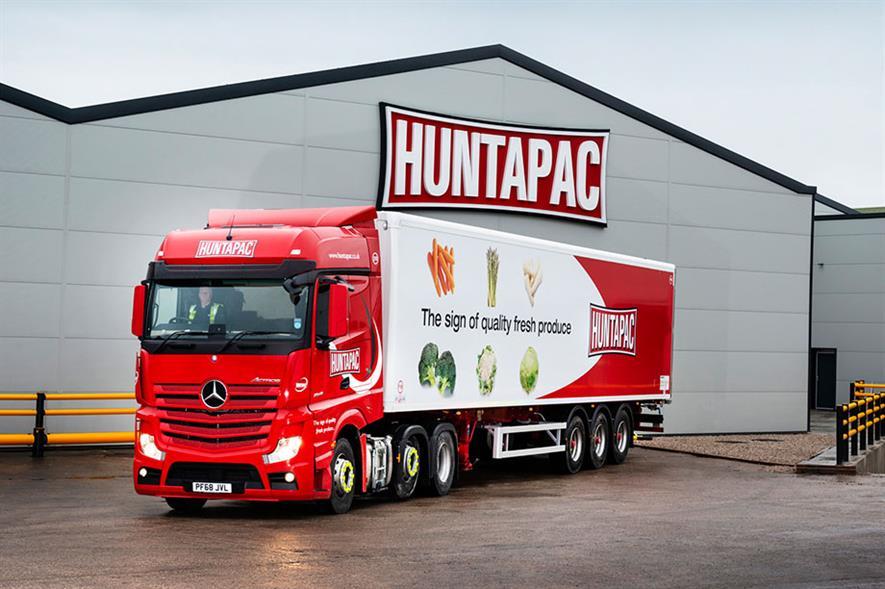
Huntapac Produce Reap Benefits from Faster Coders and TrueType Fonts
One of the leading supermarkets Huntapac supplies required it to print a new, impactful font on all its products. Becaus...
Read Success Story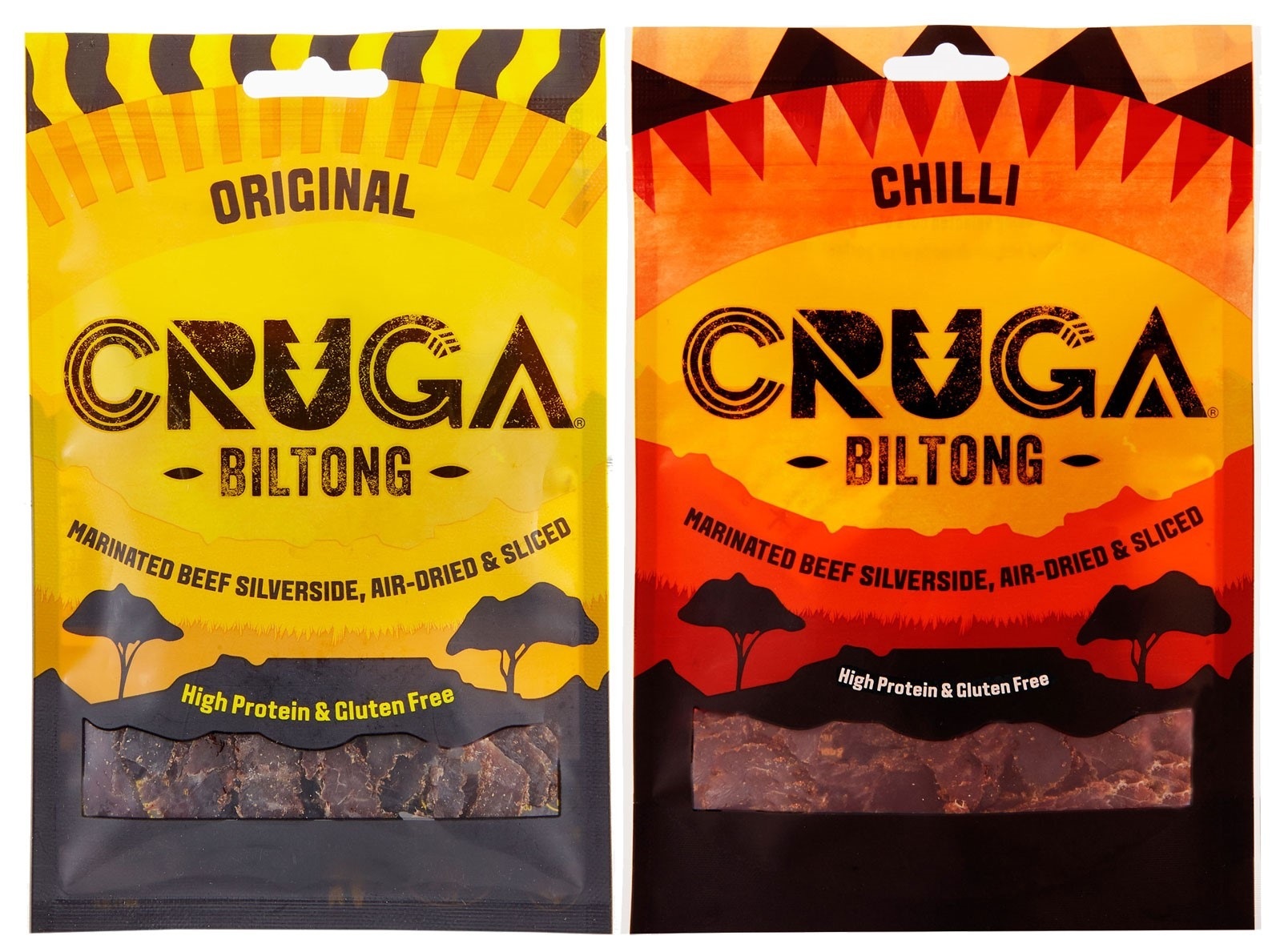
Cruga Biltong Improve Packing Efficiency with ICE Coders
To reduce packaging costs, Cruga chose to use a range of generic pouches and an ICE Zodiac Thermal Transfer Overprinter ...
Read Success StoryFAQs
Do you supply training?
Yes, we do!
We recommend training at Clearmark HQ – bespoke facilities which include test rigs to gain hands-on experience to help with maintenance and identifying parts, attendees would not be distracted, gives the opportunity to meet Clearmark staff members & fellow engineers/operators.
Scheduled days here at ICE are usually from 9am - 4pm, lunch provided, discounted hotel rates available if required. Certificate provided at the end of training days. Demo room available to show other technologies.
If we were coming to site for training, we would need to ensure that the line is available and that there is a training room the engineer could use.
If you would like to book some training or have any questions, please contact our Aftercare team by email at enquiries@uk.interactivecoding.com or call on 01159 640 144.
When you contact us, please confirm the following:
– What machine(s) do you need training for? E.g., Zodiac, Viper, Vulcan or Clarisoft software training?
– If you require training for Hawk or Zodiac, would you like standard 1-day or advanced 2-day course?
– Is engineer or operator training required?
– Do you need on-site or in-house training?
– How many attendees will need to be trained?
Do you sell labels?
Yes, we offer packages of ribbon and labels based on planned production to ensure that you have matched quantities on site.
If you would like to order labels or have any questions, please contact our Aftercare team by email at enquiries@uk.interactivecoding.com or call on 01159 640 144.
If you have a Vulcan machine, please provide the following details:
– Company details
– Contact details
– Serial number(s) of your Vulcan coder(s)
We also provide labels for other models. If you have a different coder, please confirm:
– Coder make and model
– Size or specification of label required
– Company details
– Contact details
Do you sell ink?
Yes, we offer a range of high-performance ink formulations for use with our Viper, Scorpion and Torus ranges to support applications in primary packaging, case and tray coding.
Please note that we only supply black ink.
If you would like to order ink or have any questions, please contact our Aftercare team by email at enquiries@uk.interactivecoding.com or call on 01159 640 144.
Please provide as much information as you can so that we can offer you the best solutions. Useful information includes:
– Is this for a new installation?
– What coder do you have? E.g., a Continuous Inkjet or Thermal Inkjet coder?
– Will you be printing on to a porous or glossy substrate?
– Do you need water-based or solvent ink?
Do you sell ribbon?
Yes, we stock an extensive portfolio of different ribbon grades, colours, width and lengths to meet your application requirements.
If you would like to order ribbon or have any questions, please contact our Aftercare team by email at enquiries@uk.interactivecoding.com or call on 01159 640 144.
Please provide as much information as you can so that we can offer you the best solutions. Useful information includes:
– Is this for a new installation?
– What coder do you have? E.g., is it Zodiac 53 mm/107mm or a Vulcan 76mm/107mm?
– What are you printing on to?
– What colour/width, length ribbon do you need?
– Are there any environmental factors? E.g., oil, water, heat, water, freezing, grease etc.
– Existing installations only: What is the serial number of your coder?
How may I place an order?
Please send your order request to us via email to enquiries@uk.interactivecoding.com
You may also call us on 01159 640 144.
However you choose to place your order, please ensure that you confirm the following details:
– Company name and address including your postcode
– Delivery address (if applicable)
– Your contact details such as phone number, mobile number and email address
– Details of the item(s) you would like to order
Our Aftercare team also provide support for consumables such as print heads, ribbons and inks, service and maintenance, Material Safety Data Sheets (MSDS) and extended warranty policies.
Brochures
Keep Updated
Subscribe to our newsletter for all the latest coding and industry news.