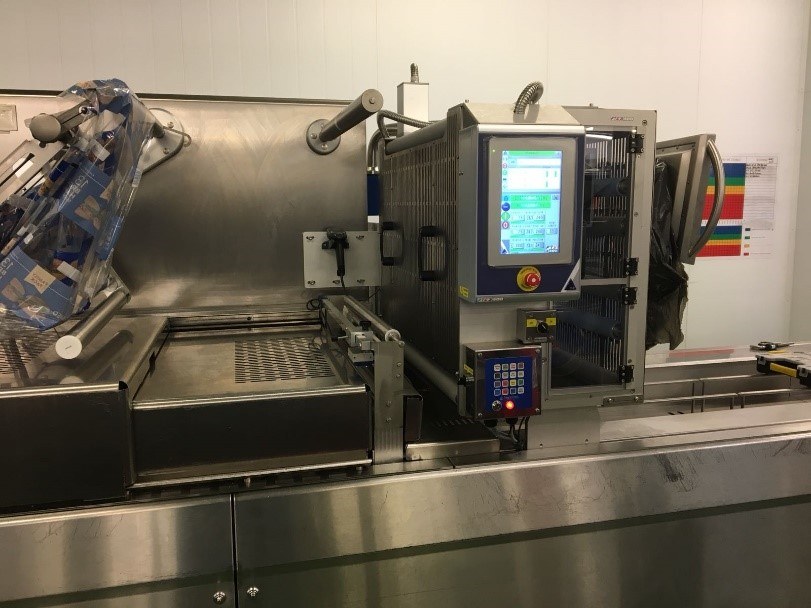
Increasing packaging machine throughput in Thermoformers
The challenge was to build a machine capable of matching a line throughput of 90 meat packs per minute that could work seamlessly alongside a thermoforming operating cycle, without compromising on print quality. The machine therefore had to be able to control the film speed during a print cycle, rather than relying on the Thermoformer print speed and being limited by the industry-wide speeds of thermal transfer printers incorporated within these systems.
ICE FTS3400 System
Award-winning innovation that paid for itself in two weeks
The ICE FTS3400 Thermal Transfer Film Transport System has been specifically engineered and constructed with the purpose of enabling the parent packaging machine (thermoformer) to operate at its designed speed without being limited by the thermal transfer printers incorporated within the system.
The intended use of the ICE FTS3400 Thermal Transfer Film Transport System is to enable the parent packaging machine to increase its throughput, while allowing the Zodiac Hawk printers incorporated within the system to print legible code information onto the packaging material at a controlled and sustained speed.
The innovative solution
The ICE FTS3400 system allows the Thermoformer to pull the film through the machine at the speed required to reach the overall machine speed set without affecting the film speed during the print cycle. The print cycle is controlled by the system during the Thermoformer “forming and sealing cycle”.
During this time the film is moved past the printers by the system shuttle and then moved back to the original starting position to enable the packaging film to be in the correct place when the Thermoformer pulls the film through to begin its next cycle.
Award-winning innovation
The project was a huge success leading to a significant productivity gain as the machine increased product cycles from 10-to-12 cycles per minute, significantly increasing throughput. This increase was so large the system paid for itself in just two weeks, and the customer has gone on to order more of the systems.
It has since been provided as a solution to three leading manufacturers in the UK facing the same challenge.
The success of the project has been recognised by the industry body, Processing and Packaging Machinery Association – winning their prestigious Innovative Ancillary Equipment category at their 2019 awards.
Chris Simpson, Managing Technical Director at Clearmark comments: “We were extremely proud to have been recognised by the PPMA as a leading coding and labelling solution provider within the industry.
“I would like to extend my gratitude to the teams involved for their continued hard work and commitment in helping our customers to overcome key industry challenges through creative and technical innovation.”
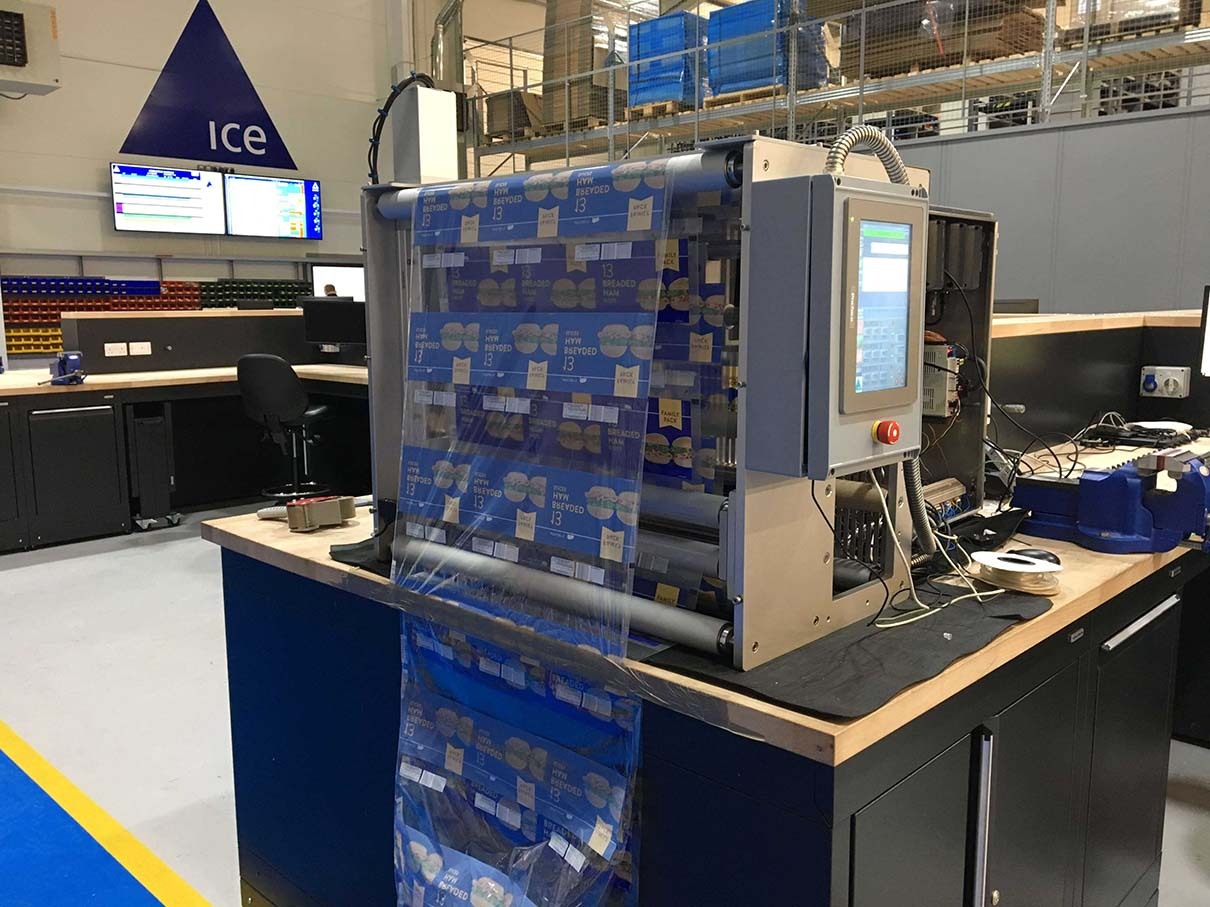
High quality codes at unprecedented speeds
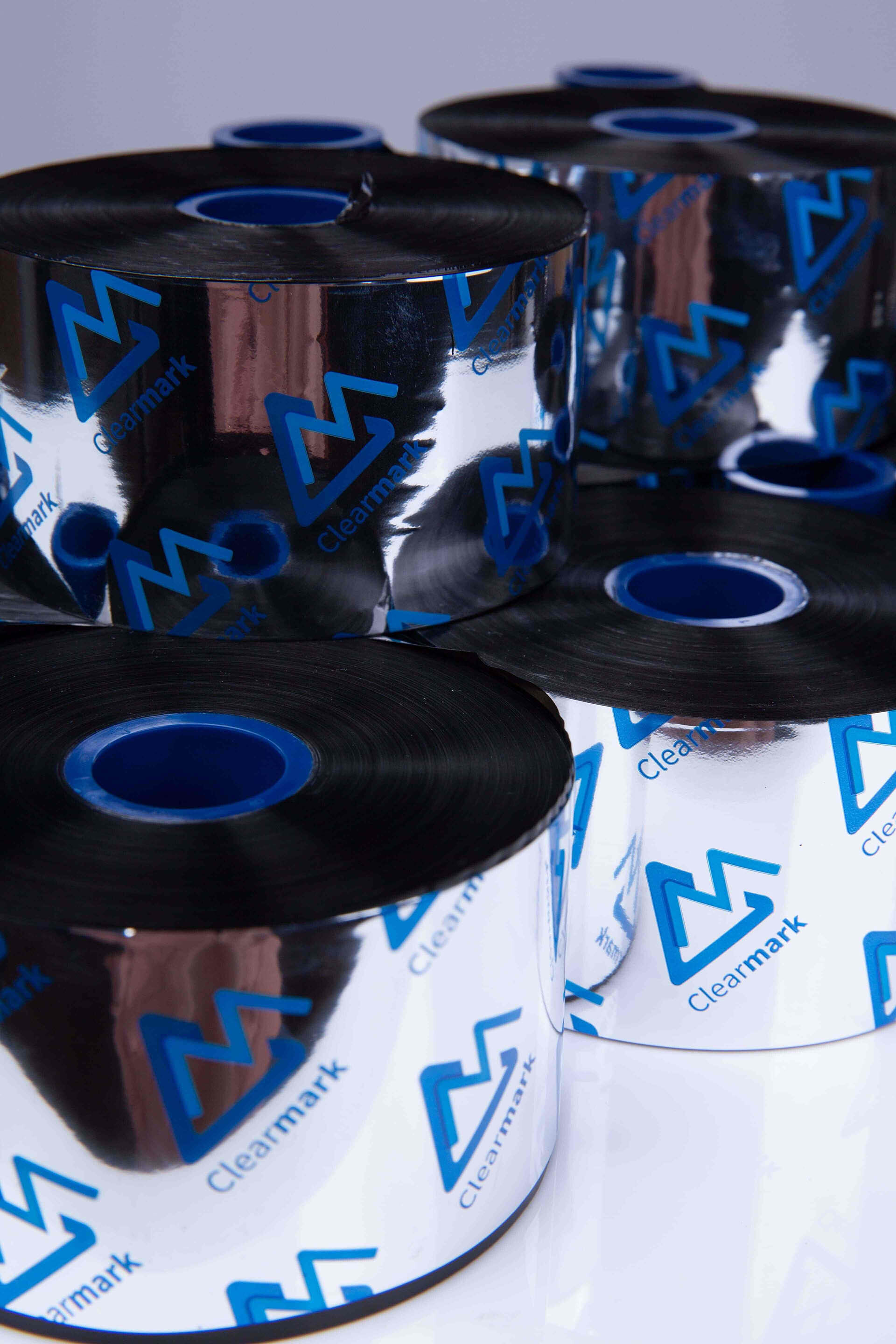
This project also required close collaboration with Clearmark’s in-house Print Lab and consumables team, to ensure that the highest-grade thermal ribbon could be extensively tested and supplied with the system in order to achieve the print quality required at limit-pushing speeds.